About this Product
Handmade Jumbo Chonk 35mm D20 dice made with resin.
This die contains glittery swirls in various shades of purple ranging from shimmery bluish purple to reddish purple depending on the lighting. The die is inked in metallic gold. It does have some minor imperfections around the "1" face but it is completely cosmetic and will not effect the rolling of the die.
This listing is for 1 single d20 die. Perfect for a game of Dungeon & Dragons or other tabletop RPG games.
Disclaimer: This die is handmade and while I do my best, it may have minor imperfections and may be imperfectly weighted.
Hickory River Designs
Meet the Maker
OUR STORY & WHERE WE COME FROM
Hi, I'm Shannon the owner of the small business Hickory River Designs. I am currently a stay at home mom of a wonderful little girl. I initially started creating pieces alongside my dad for our own homes as a way express ourselves and bring life to our ideas. We recently decided to start a new chapter and take our hobby and begin our journey as a small business.
We repurpose the majority of our wood from fallen down trees on our family-owned property, here in Eastern Pennsylvania. The remaining wood is collected from other neighboring properties that no longer need the wood after cleaning up their yards. We run the wood through our sawmill directly on our property to cut up each of the logs. Each piece of wood then goes through an extensive drying process that can take up to a year or more depending on how thick it is cut. We proceed to plane the wood and carve it using a CNC machine or lathe for bowls/vases. We also incorporate epoxy resin to some of our pieces as well. Each piece is then finished with a protective sealer.
Each item you find in our store has been handcrafted by us in our at home shop. We love creating different varieties of pieces that can be treasured for many years. We take great pride in creating our items with the same care and attention that we expect when buying pieces for our own home.
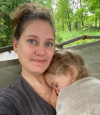
How it’s Made
When I was first looking into making handmade resin dice, I did some looking around to see what was already out there, and one of the first things I thought to myself was "Wow! Handmade dice are so expensive!" Well, turns out dice making takes a lot of time and precision, requires a lot of specialized equipment, and are essentially tiny pieces of art.
Let’s walk through the steps it takes to make a set of dice.
The first step is setting up and pouring the dice (my favorite part). I have to get all the materials together and placed where they need to go. I then stir the resin for 4 minutes and after the resin is thoroughly mixed and all the streaks are gone, I then add all the different colors and inclusions (glitter, flakes, fibers, etc.) After each of the colors are mixed in, all the resin gets put into a vacuum chamber for 10 minutes which removes air bubbles that were created during the mixing process. Then it’s finally time to pour the resin into the dice mold, which takes a bit of time as well! At minimum, pouring three sets takes about two hours to do, although it can definitely take longer! (But let’s say each set takes 45 minutes minimum to pour).
Next, I put the dice in a pressure pot to cure for 24 hours under about 32 psi of pressure. This takes all of the remaining air bubbles in the resin that the vacuum chamber didn’t get and squishes them down until they're so small they can't even be seen. This results in crystal clear resin that is bubble free!
After the 24 hours of curing are up, the molds can be removed from the pressure pot, and the dice can be removed from the molds. This is the fun part, I finally get to see how the dice turned out! It takes me about 5min to do.
The dice then sit for another 3 + days to finish curing completely.
After the dice have fully cured, I move on to sanding and polishing. First, I use a low grit sandpaper to get off all the lips, bumps, and any raised faces off. I then move on to hand sanding in various grits going all the way up to 7000. I then go through a set of polishing papers to get the dice to a nice finish on the sides that needed sanding. The whole sanding process takes me roughly 1 ½ hours or more per set of dice.
These roughly polished dice then get put into a vibratory tumbler with some plastic polish and ceramic media and are left to polish for about a week and a half. I check the dice 2-3 times a day to see how they are doing and add more polish to the tumbler. Overall, I would estimate that all the checking and refreshing takes me about 30 minutes per set of dice.
Once they are all polished, the dice get pulled out of the tumbler and put into a bowl of warm soapy water and then into an ultrasonic jewelry cleaner for 10 minutes per set. Afterwards, I scrub them with a soft toothbrush. The numbers of the dice get filled with a lot of gunk from the sanding (resin dust) and polishing (excess polish) and it needs cleaned out. This takes me about 30 minutes per set.
This leads on to the last step of finishing the dice which is inking (filing in the numbers). I ink my dice with acrylic paint using a small paintbrush and then wipe excess paint off the surface of each face with a paper towel. It's always amazing to me how much the number color can affect the feel of a set of dice; it's like magic! Inking a set of dice takes me about 45 minutes.
So overall, between 45 mins pouring, 5 mins unmolding, 90 mins sanding, 30 mins refreshing the polishing tumblers, 40 mins cleaning, and 45min inking, that brings us to roughly 4 hours of work time per set of dice (minimum). And that doesn't even take into account making the molds (they take a couple hours to make), making inclusions to be put in the dice, cleaning up the workspace, packaging items to be shipped, and of course all the equipment, tools, and materials needed to make resin dice.
Shop Policies
Returns and cancellations are accepted if the following conditions are met:
Contact us within 3 days of delivery
Ship items back within 7 days of delivery
Request a cancellation within 2 hours of purchase
If there is a problem with the order that you have received, please contact me via email. My descriptions and photos are as accurate as I can get them with my camera and lighting, there may be a slight color difference in what you receive as opposed to the picture due to lighting. Please take your time when reading my descriptions and before ordering, if you are unsure about anything, please message with any questions you may have before placing the order. I try to give accurate descriptions and do not want you to be disappointed when you receive your product. I'm happy to answer any inquiries prior to your purchase, communication is key for a happy purchase for both the of us. If an item arrives damaged, please let me know as soon as possible.
Conditions of return:
PLEASE DO NOT SEND THE ITEM BACK BEFORE CONTACTING ME. The item MUST be shipped back to me in the original package, using the same shipping method by which it was shipped to you. You will need to provide me with the Tracking Number of the package once you have shipped it. Once I receive the item, I will make an exchange, repair, or refund.
Buyers are responsible for the cost of shipping charges for the return. If the item is not returned in its original condition, the buyer is responsible for any loss in value.
To start a return, contact us at HickoryRiverDesigns@gmail.com. If your return is accepted, we'll give you instructions on how and where to send your package. We will notify you once we’ve received and inspected your return, and you’ll be refunded on your original payment method. Please remember it can take some time for your bank or credit card company to process and post the refund too.
Damaged and Missing Items:
Please inspect your order upon reception and contact us immediately if the item is defective, damaged or if you receive the wrong item, so that we can evaluate the issue and make it right. If you never received your order, please contact us at HickoryRiverDesigns@gmail.com or reach out to your shipping carrier so that the package can be found. If your order is still missing after taking these steps, please let us know so a refund can be issued.
This policy was last modified on 10.04.2024